Step 1
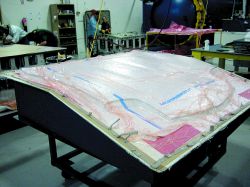
Following automated ply cutting, plies three through six of the hood outer panel are consolidated under vacuum on a male-form preform tool. Source: MacLean Quality Composites
|
Step 2
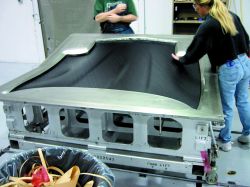
After application of mold release, the first two plies of prepreg are layed into the mold by hand, followed by the remaining four-ply preform. Source: MacLean Quality Composites
|
Step 3
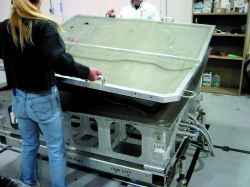
A formed silicone vacuum bag is used to evacuate the air. The reusable bag saves time and results in a smoother part surface than a disposable bagging. Source: MacLean Quality Composites
|
Step 4
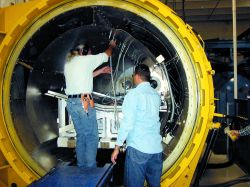
The prepreg is cured in an autoclave at 100 psi and 150°C/302°F. The cycle time in the autoclave is approximately two hours, including heating, cure and cooling. Source: MacLean Quality Composites
|
Step 5
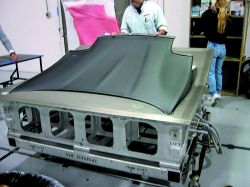
Following cure, the carbon fiber hood outer panels are demolded and the edges trimmed on a 5-axis CNC router. Source: MacLean Quality Composites
|
Step 6
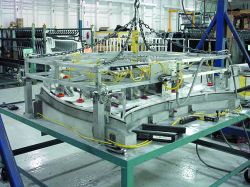
The inner and outer panels are bonded together in a vacuum fixture using a room-temperature, two-part polyurethane structural adhesive. Source: MacLean Quality Composites
|
Step 7
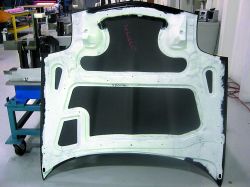
The bonded hood assembly shows the compression molded inner panel, supplied by Meridian Automotive Systems. Low-density SMC (light gray) is co-molded with carbon fiber SMC (perimeter of inner panel). Source: MacLean Quality Composites
|
Step 8
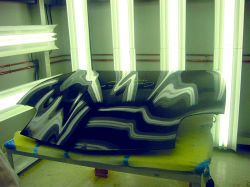
The assembled hood is inspected for dimensions, and then for surface quality in a specially designed light room. If required, surface defects are repaired prior to application of primer. Source: MacLean Quality Composites
|